HomeWe hope you enjoy this abbreviated version of the
Frankenmuth News
Serving Frankenmuth Since 1906
Vol. 119 No. 52 In our 119th year!
Wednesday, July 2, 2025
----------------------------------------------------------------------------------------------------
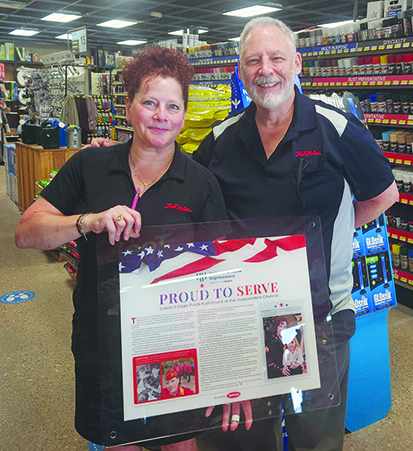
CASSIE CIRISAN . . . store manager at Frankenmuth True Value Hardware, was recently recognized by the North American Hardware and Paint Association. Above, she accepts her framed honor from True Value Retail Business Partner Patrick O'Malley.
Cassie Cirisan honored by NHPA's Helmets to Home Improvement program
Former Marine now store manager at True Value Hardware
Frankenmuth True Value is proud to announce that Store Manager Cassie Cirisan has been named a featured honoree in the North American Hardware and Paint Association’s (NHPA) prestigious Helmets to Home Improvement program.
This new initiative celebrates military veterans who have transitioned from serving their country to making meaningful contributions in the home improvement industry.
Cirisan, a United States Marine Corps veteran who served from 1990 to 1998, was honored Friday, June 27, at the store, with special framed tribute to her. She was recognized not only for her military service, but also for her leadership and impact in the independent hardware retail channel.
As one of the few women in her Marine Corps aviation ordinance unit, where she rose to the rank of sergeant, Cassie thrived in a challenging environment, working on both fighter jets and helicopters, and gaining invaluable experience and perspective.
“Serving in the Marines taught me how to get things done with whatever is at hand,” Cirisan said. “That is a skill I use everyday in our store – solving problems creatively and helping our customers find their best solutions.”
Following her service to America, Cirisan entered the hardware industry in 2002 and brought her hands-on, mission-focused approach to Frankenmuth True Value in 2015 – a decade ago. She quickly rose to store manager and has since helped build the store to a go-to destination for paint, hardware, and friendly knowledgeable service. ........
.....To read this complete story and other featured articles in this week's Frankenmuth News, click on the "Subscribe" tab at the left or call (989-652-3246) to begin receiving your weekly copy of the Frankenmuth News.
4044043
|